1. dyMat ®Green product
PET-based backsheets have more sustainable end-of-life (EOL) possibilities compared to fluorinated backsheets for which the only viable disposable method is landfill, creating great damage to the environment because of the pollution generated and the release of toxic substances into the environment.
PET-based backsheets meanwhile can be disposed of in different ways:
- Incineration: during the combustion process new energy is generated but there are still risks of toxic substances being release into the environment.
- Pyrolysis: during this more virtuous process new electricity and also new fuel are generated.
- Monomer recycling: at the end of their life cycle the backsheets undergo a recycling process bring the PET back into a monomer state which can then be repolymerized to become recycled polyester (rPET). See also chapter 3: Coveme Circular economy project.
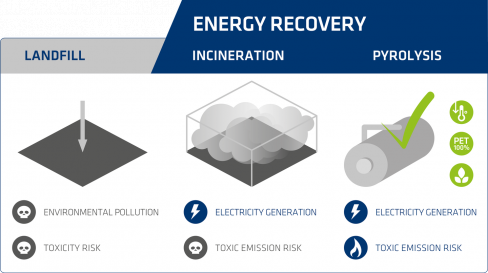
Fraunhofer UMSICHT study:
Coveme commissioned the Fraunhofer UMSICHT Institute to conduct an in-depth study to analyse the impact of PET based backsheets in landfill, incineration and pyrolysis compared to fluorinated backsheets.
- Incineration experiment: the study shows that the incineration of fluorinated backsheets generates toxic contaminants such as hydrofluoric acid (HF), fluoroalkanes and contaminated particulate matter which are highly harmful to the environment.
- Pyrolysis experiment: the study confirms that the pyrolysis of fluoropolymers (such as TPT, KPK) is not a viable path because all three elements generated by pyrolysis, that is pyrolysis gas, pyrolysis oil and pyrolysis carbon, are contaminated by dangerous halogenated components and therefore make them unusable for the traditional applications envisaged.
In conclusion, the Fraunhofer UMSICHT study shows that the LCA for the PET-based backsheet (without fluorine) shows excellent results compared to the fluorinated backsheet for both incineration and pyrolysis and therefore the use of fluoropolymers or halogenated polymers in PV modules should be avoided and at the same time the use of PET-based backsheets should be encouraged.
TO READ THE FULL STUDY CLICK HERE